Intelligent cooling.
Sustainable savings.
With our technology, you can reduce your cold storage energy costs by up to 40% – thanks to AI-based refrigeration control, precise sensor technology, and optimized energy flow management.
Intelligent cooling.
Sustainable savings.
With our technology, you can reduce your cold storage energy costs by up to 40% – thanks to AI-based refrigeration control, precise sensor technology, and optimized energy flow management.
Cooling is expensive. And often invisibly inefficient.
Cooling is a vital part of the logistics chain in the food industry. However, refrigeration is prone to disruptions and costly to operate: cold storage can account for up to 85% of a company’s energy costs. Energy consumption is particularly high in deep-freeze operations, not only because of the immense physical effort required to lower the temperature, but also because evaporators frequently ice up, making energy-intensive defrosting procedures necessary.
Our solution:
A self-learning, intelligent refrigeration control system
Coldsense connects sensors, data, and AI to create an intelligent nervous system that monitors the entire cold storage environment in real time – temperature, icing, energy flows, and user behavior. It detects changes, responds immediately, and learns with every signal.
The result:
Measurably greater efficiency in cold storage
40% lower energy costs
Defrosting occurs only when it is truly necessary.
Lower maintenance costs
360° monitoring with reliable icing protection
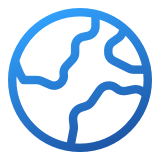
Improved carbon footprint
Key figures in monthly reports document your successes.
Example calculation: How intelligent refrigeration control reduces your energy consumption
Coldsense technologies are suitable for all types of refrigeration systems – across all industrial sectors: from the food industry to low-temperature applications in the chemical and pharmaceutical sectors, as well as climate chamber applications in the automotive industry. The fundamental Coldsense principle can be applied to any area of use. We support both the retrofitting of existing systems and the implementation in new installations. The use of Coldsense technologies pays off quickly:
Cold storage facility with freezers, deep-freeze and normal refrigeration rooms, total cooling capacity
of 304 kWElectrical connected load of the refrigeration system: 92 kW.
Efficiency increase of the refrigeration system through our technology: 20.3%
Annual electricity savings: 163,602 kWh
What our customers say
A well-rounded solution: Our technology and service package
Our system solution is based on a combination of hardware (technology) and data-based services (service). The technology package includes all sensors and materials required for monitoring and intelligent control of the refrigeration system. The service package includes the refinement, analysis and interpretation of the acquired sensor data.
Some of our trusted clients
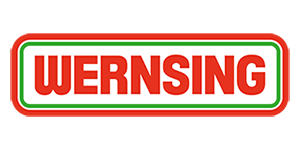
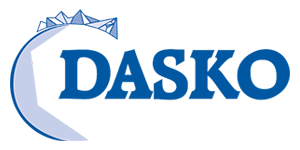
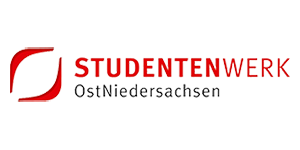
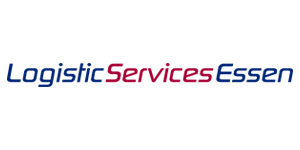
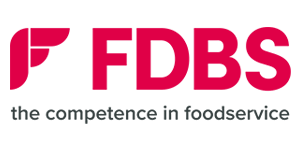
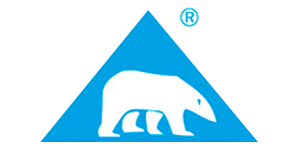
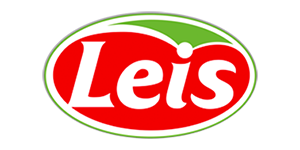
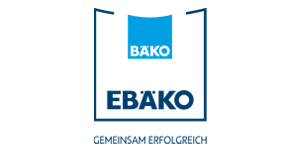
Our locations
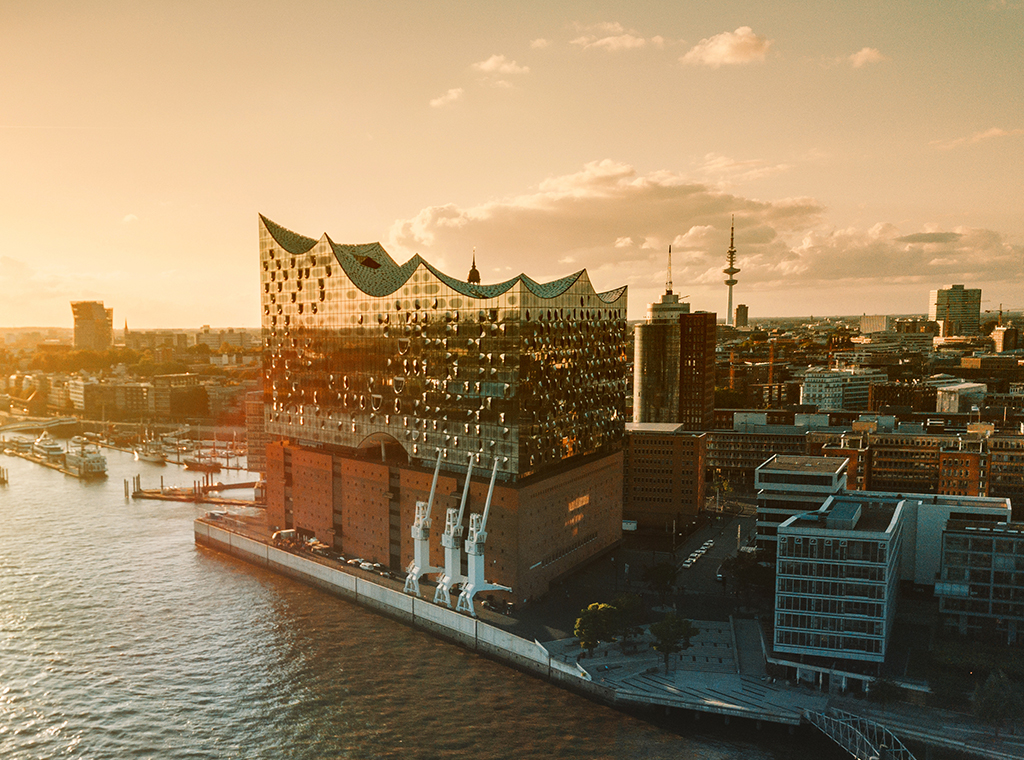
Coldsense Technologies GmbH – Company Headquarters
Bella-Spanier-Weg 6, 20097 Hamburg, Deutschland
Bella-Spanier-Weg 6, 20097 Hamburg, Deutschland
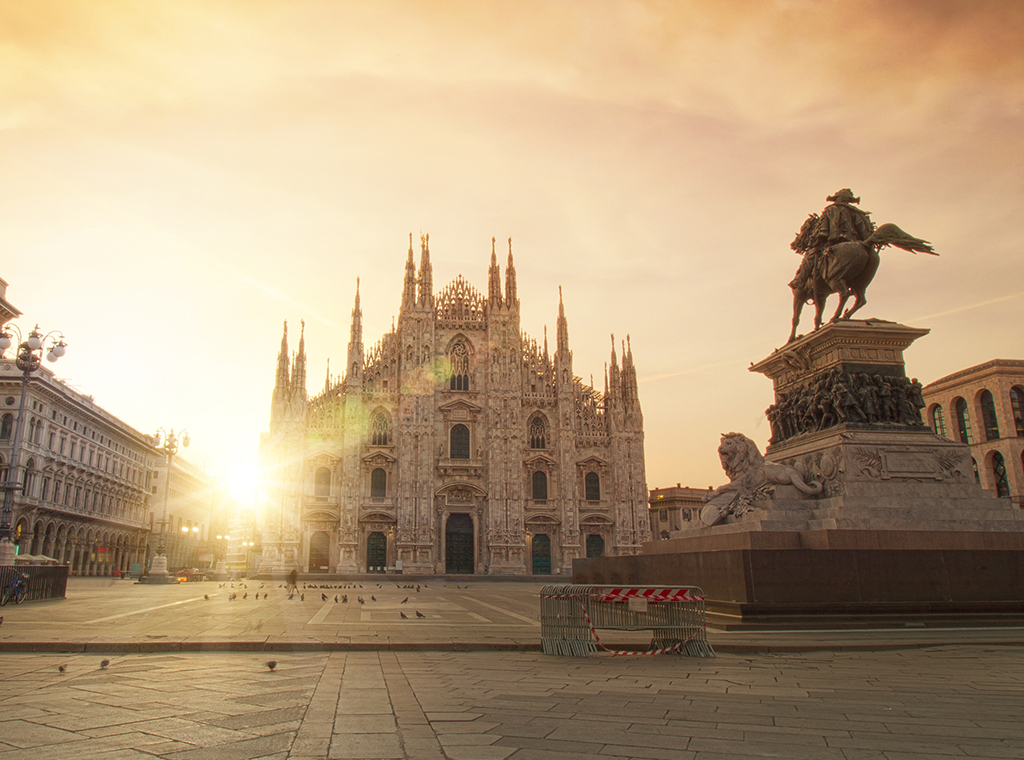
Coldsense Technologies GmbH – Office in Italy
Via Giuseppe Piazzi 2-4, 20159 Milano (MI), Italy
Via Giuseppe Piazzi 2-4, 20159 Milano (MI), Italy
Knowledge Store
For energy consultants
Do your customers run cold rooms? Read here why you should recommend Coldsense technology to reduce electricity costs.
For system engineers
Find out here what advantages AI-controlled defrosting offers for planning refrigeration systems – and how it simplifies your day-to-day work.
How can we support you?
Contact us now for a free initial consultation – we look forward to a personal exchange with you! We would be happy to answer all your questions about AI-controlled cold room defrosting and show how your company can benefit from Coldsense technology.